Термическая обработка металлов. Композиционные материалы
Термическая обработка металлов. Композиционные
материалы
Реферат по дисциплине «Материаловедение» выполнил
Ковалёв В.В.
Тираспольский межрегиональный университет
Типасполь, 2005
1. Теория и технология термической обработки. Виды
термической обработки. Отжиг, нормализация, закалка, старение, улучшение.
Термической
обработкой называют процессы, связанные с нагревом и охлаждением, вызывающие
изменения внутреннего строения сплава, и в связи с этим изменения физических,
механических и других свойств.
Термической
обработке подвергают полуфабрикаты (заготовки, поковки, штамповки и т. п.) для
улучшения структуры, снижения твердости, улучшения обрабатываемости, и
окончательно изготовленные детали и инструмент для придания им требуемых
свойств.
В
результате термической обработки свойства сплавов могут меняться в широких
пределах. Например, можно получить любую твердость стали от 150 до 250 НВ
(исходное состояние) до 600—650 НВ (после закалки). Возможность значительного
повышения механических свойств с помощью термической обработки по сравнению с
исходным состоянием позволяет увеличить допускаемые напряжения, а также
уменьшить размеры и вес детали.
Основоположником
теории термической обработки является выдающийся русский ученый Д. К. Чернов,
который в середине XIX в., наблюдая изменение цвета каления стали при ее
нагреве и охлаждении и регистрируя температуру «на глаз», обнаружил критические
точки (точки Чернова).
Основными
видами термической обработки стали являются отжиг, нормализация, закалка и
отпуск.
Отжиг.
Отжигом называют операцию нагрева, выдержки при заданной температуре и
охлаждения заготовок. Академик А. А. Бочвар дал определение двух родов отжига:
отжиг первого рода — приведение структуры из неравновесного состояния в более
равновесное (возврат или отдых, рекристаллизационный отжиг, или
рекристаллизация, отжиг для снятия внутренних напряжений и диффузионный отжиг
или гомогенизация); отжиг второго рода — изменение структуры сплава посредством
перекристаллизации около критических точек с целью получения равновесных
структур; к отжигу второго рода относятся полный, неполный и изотермический
отжиги.
Рассмотрим
виды отжига применительно к стали.
Возврат
стали — нагрев до температуры 200—400 °С для уменьшения или снятия наклепа. При
возврате наблюдается уменьшение искажений в кристаллических решетках у
кристаллов и частичное восстановление физико-химических свойств.
Рекристаллизационный
отжиг (рекристаллизация) стали происходит при температуре 500—550 °С; отжиг для
снятия внутренних напряжений — при температуре 600—700 °С. Эти виды отжига
применяют для заготовок, обработанных давлением (прокаткой, волочением, ковкой,
штамповкой). При рекристаллизационном отжиге деформированные вытянутые зерна
становятся равноосными, в результате твердость снижается, а пластичность и
ударная вязкость повышаются. Для полного снятия внутренних напряжений в стали
нужна температура не менее 600 °С.
Охлаждение
после выдержки при заданной температуре должно быть достаточно медленным; при
ускоренном охлаждении вновь возникают внутренние напряжения.
Диффузионный
отжиг применяют в тех случаях, когда в стальных заготовках имеется
внутрикристаллическая ликвация. Выравнивание состава в зернах аустенита
достигается диффузией углерода и других компонентов наряду с самодиффузией
железа. В результате сталь становится однородной по составу (гомогенной),
поэтому диффузионный отжиг называется также гомогенизацией.
Температура
гомогенизации должна быть достаточно высокой (1100 -1200 °С), однако нельзя
допускать пережога и оплавления зёрен. При пережоге кислород воздуха окисляет
железо, проникает в толщу его, в результате образуются кристаллиты, разобщенные
оксидными оболочками. Пережжённые заготовки являются неисправимым браком.
При
полном отжиге понижаются твердость и прочность стали; этот отжиг связан с
фазовой перекристаллизацией при температурах точек Ас1 и Ac3. В результате
полного отжига структура стали становится близкой к равновесной, что
способствует лучшей обрабатываемости резанием и штамповкой. Полный отжиг
используют также как окончательную операцию термической обработки заготовок.
Для полного отжига сталь нагревают на 30—50° выше температуры линии GSK и
медленно охлаждают. Операция выполняется с охлаждением заготовок в печи при
частичном подогреве, чтобы скорость охлаждения былa в пределах 10—100 °С/ч для
легированной стали и 150—200 оС/ч для углеродистой стали.
Отжигом
достигается также измельчение зерна. Крупнозернистая структура получается,
например, в результате перегрева стали, такая структура называется
видманштетовой. На рис. 1 приведена видманштетовая структура доэвтектоидной
стали (х50); она характерна расположением феррита (светлые участки) и перлита в
виде вытянутых пластин под различными углами друг к другу.
В
заэвтектоидных сталях видманштетовая структура
характеризуется штрихообразным расположением
избыточного цементита.
Неполный
отжиг связан с фазовой перекристаллизацией
лишь при температуре точки Ас1, его
применяют после горячей обработки
давлением, когда у заготовок мелкозернистая
структура.
Для
доэвтектоидной стали этот отжиг Рис. 1. используют в целях улучшения обрабатываемости резанием.
Отжиг
на зернистый перлит служит для повышения пластичности и вязкости стали и
уменьшения ее твердости. Для получения зернистого перлита заготовки нагревают
несколько выше точки Ac1 и выдерживают недолго, чтобы цементит растворился в
аустените не полностью. Затем производят охлаждение до температуры несколько
ниже Аr1 и выдерживают при такой температуре несколько часов.
При
изотермическом отжиге после нагрева и выдержки заготовки быстро охлаждают до
температуры несколько ниже точки Аr1 и выдерживают при этой температуре до
полного распада аустенита в перлит, после чего охлаждают на воздухе. Применение
изотермического отжига обеспечивавает повышение производительности труда,
например, обычный отжиг легированной стали длится 13-15 ч, а изотермический –
4-7 ч.
Нормализация.
При нормализации сталь после нагрева охлаждается не в печи, а на воздухе в цехе,
что экономичнее. Нагрев ведется до полной перекристаллизации (на 30—50° выше
точек Ас3, и Аст); в результате нормализации сталь приобретает мелкозернистую и
однородную структуру. Твердость и прочность стали после нормализации выше, чем
после отжига. Структура низкоуглеродистой стали после нормализации
ферритно-перлитная, но более дисперсная, чем после отжига, а у средне- и
высокоуглеродистой сталей — сорбитная; нормализация может заменить для первой
отжиг, а для вторых — закалку с высоким отпуском. Часто нормализацией улучшают
структуру перед закалкой.
Закалка и отпуск стали.
Целью
закалки и отпуска стали является повышение твердости и прочности. Закалка и
отпуск стали необходимы для очень многих деталей и изделий. Закалка основана на
перекристаллизации при нагреве и предотвращении перехода аустенита в перлит
путем быстрого охлаждения. Закаленная сталь имеет неравновесную структуру мартенсита,
троостита или сорбита.
Чаще
всего сталь резко охлаждают на мартенсит. Для смягчения действия закалки сталь
отпускают, нагревая до температуры ниже точки А1. При отпуске структура стали
из мартенсита закалки переходит мартенсит отпуска, троостит отпуска, сорбит
отпуска.
Закалка
стали. Температура нагрева стали при закалке та же, что и при полном отжиге:
для доэвтектоидной стали на 30—50 °С выше точки Ас3, для заэвтектоидной — на
30—50° выше точки Aс1. При нагреве доэвтектоидной стали до температуры между
точками Ас1 и Ac3 (неполная закалка) в структуре быстро охлажденной стали
наряду с закаленными участками будет присутствовать нерастворенный при нагреве
(в аустените) феррит, резко снижающий твердость и прочность. Поэтому для
доэвтектоидной стали обязательна полная закалка с нагревом выше точки Ас3.
В
заэвтектоидной стали избыточной фазой является цементит, который по твердости
не уступает мартенситу и даже превосходит его, поэтому сталь достаточно нагреть
на 30—50 °С выше точки Ас1.
Нагревать
заготовки, особенно крупные, нужно постепенно во избежание местных напряжений и
трещин, а время выдержки нагретых заготовок должно быть достаточным, чтобы
переход в структуру аустенита полностью завершился.
Скорость
охлаждения заготовок при закалке должна быть такой, чтобы получить заданную
структуру. Критическая скорость закалки изменяется в широких пределах в
зависимости от наличия легирующих компонентов в стали. Для простых сплавов
железо—углерод эта скорость очень высока. Присутствие в стали кремния и
марганца облегчает закалку на мартенсит, так как для такой стали С-образные
кривые на диаграмме изотермического превращения аустенита будут сдвинуты вправо
и критическая скорость закалки понижается.
Наиболее
распространено охлаждение заготовок погружением их в воду, в щелочные растворы
воды, в масло, расплавленные соли и т. д. При этом сталь закаливается на
мартенсит или на бейнит.
При
закалке применяют различные способы охлаждения в зависимости от марки стали,
формы и размеров заготовки.
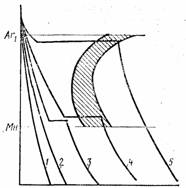
Простую
закалку в одном охладителе (чаще всего в воде или водных растворах) выполняют,
погружая в него заготовки до полного охлаждения.
На рис. 2 режим охлаждения при такой закалке
характеризует кривая 1.
Для
получения наибольшей глубины закаленного
слоя применяют охлаждение при
интенсивном обрызгивании.
Прерывистой
закалкой называют такую, при которой
заготовку охлаждают последовательно в
двух средах: первая среда — охлаждающая
жидкость (обычно вода), вторая — воздух
или масло (см. кривую 2 на рис. 2).
Резкость такой закалки меньше, чем
предыдущей. Рис. 2.
При
ступенчатой закалке заготовку быстро погружают в соляной расплав и охлаждают до
температуры несколько выше Мн. Выдержка обеспечивает выравнивание температуры
от поверхности к сердцевине заготовки, что уменьшает напряжения, возникающие
при мартенситном превращении; затем заготовку охлаждают на воздухе (кривая 3 на
рис. 2).
Изотермическая
закалка (закалка в горячих средах) основана на изотермическом распадении
аустенита. Охлаждение ведется до температуры несколько выше начала
мартенситного превращения (200—300 °С) в зависимости от марки стали. В качестве
охладителя используют соленые расплавы или масло, нагретое до 200—250 °С. При
температуре горячей ванны заготовка выдерживается продолжительное время, пока
пройдет инкубационный период и период превращения аустенита (кривая 4 на рис.
2). В результате получается структура бейнита, по твердости близкая к
мартенситу, но более вязкая и пластичная. Последующее охлаждение производится
на воздухе.
При
изотермической закалке вначале требуется быстрое охлаждение со скоростью не
менее критической, чтобы избежать распадения аустенита. Следовательно, по этому
методу можно закаливать лишь небольшие (диаметром примерно до 8 мм) заготовки
из углеродистой стали, так как массивные заготовки не удается быстро охладить.
Это не относится однако к легированным сталям, большинство марок которых имеют
значительно меньшие критические скорости закалки. Большим преимуществом
изотермической закалки является возможность рихтовки (выправления искривлений)
заготовок во время инкубационного периода превращения аустенита (который длится
несколько минут), когда сталь еще пластична.
Закалка
при помощи газовой горелки. Кислородно-ацетиленовое пламя газовой горелки с
температурой около 3200 °С направляется на поверхность закаливаемой заготовки и
быстро нагревает ее поверхностный слой до температуры выше критической. Вслед
за горелкой перемещается трубка, из которой на поверхность заготовки
направляется струя воды, закаливая нагретый слой. Этот способ применяется для
изделий с большой поверхностью (например, для прокатных валков, зубьев больших
шестерен и т. д.).
Закалка
токами высокой частоты по методу В. П. Вологдина нашла очень широкое применение
в промышленности, так как отличается высокой производительностью, легко
поддается автоматизации.
Обработка
холодом. Этот метод применяется для повышения твердости стали путем перевода
остаточного аустенита закаленной стали в мартенсит. Холодом обрабатывают
углеродистую сталь, содержащую больше 0,5 % С, у которой температура конца
мартен-ситного превращения находится ниже 00 С, а также легированную сталь
(например, быстрорежущую).
Отпуск
стали. Отпуск смягчает действие закалки, снимает или уменьшает остаточные
напряжения, повышает вязкость, уменьшает твердость и хрупкость стали. Отпуск
производится путем нагрева заготовок до температуры ниже критической; при этом
в зависимости от температуры могут быть получены структуры мартенсита,
троостита или сорбита отпуска.
При
низком отпуске (нагрев до температуры 150—200 °С) в структуре стали в основном
остается мартенсит, который однако имеет другую решетку, как сказано выше.
Кроме того, начинается выделение карбидов железа из пересыщенного твердого
раствора углерода в a-железе
и начальное скопление их небольшими группами. Это влечет за собой некоторое
уменьшение твердости и увеличение вязкости стали, а также уменьшение внутренних
напряжений в заготовках. Для низкого отпуска, заготовки выдерживают в течение
определенного времени обычно в масляных или солевых ваннах. Если для низкого
отпуска заготовки нагревают в атмосфере воздуха, то для контроля температуры
часто пользуются цветами побежалости, появляющимися на зачищенной поверхности
заготовки. Появление этих цветов связано с интерференцией белого цвета в
пленках оксида железа, возникающих на поверхности заготовки при ее нагреве. Для
углеродистой стали в интервале температур от 220 до 330 °С в зависимости от
толщины пленки цвет изменяется от светло-желтого до серого. Для легированной
стали соответствующие температуры выше. Низкий отпуск применяют для режущего
инструмента из углеродистых и легированных сталей, измерительного инструмента,
цементированных заготовок, а также других изделий, работающих в условиях трения
на износ.
При
среднем (нагрев в пределах 300—500 °С) и высоком (500—700 °С) отпуске структура
мартенсита переходит соответственно в структуру троостита или сорбита. Чем выше
температура отпуска, тем меньше твердость отпущенной стали и тем больше ее
вязкость. При высоком отпуске сталь получает наилучшее сочетание механических
свойств: повышенные прочность, вязкость и пластичность; поэтому закалку на
мартенсит с последующим высоким отпуском называют улучшением стали. Средний
отпуск применяют при производстве кузнечных штампов, пружин, рессор, а
высокий—для многих деталей, подверженных действию высоких напряжений (например,
осей автомобилей, шатунов двигателей).
2. Химико – термическая обработка. Её виды.
Целью
химико-термической обработки является получение поверхностного слоя стальных
изделий, обладающего повышенными твердостью, износоустойчивостью,
жаростойкостью или коррозионной стойкостью. Для этого нагретые заготовки
подвергают воздействию среды, из которой путем диффузии в поверхностный слой
заготовок переходят нужные для получения заданных свойств элементы: углерод,
азот, алюминии, хром, кремний и др.
Эти
элементы диффундируют в поверхностный слой лучше, когда они выделяются в
атомарном состоянии при разложении какого-либо соединения. Подобное разложение
легче всего происходит в газах, поэтому их и стремятся применять для
химико-термической обработки стали. Выделяющийся при разложении газа
активизированный атом элемента проникает в решетку кристаллов стали и образует
твердый раствор или химическое соединение. Наиболее распространенными видами
химико-термической обработки стали являются цементация, азотирование,
цианирование.
Цементация.
Цементацией называется поглощение углерода поверхностным слоем заготовки,
который после закалки становится твердым; в сердцевине за готовка остается
вязкой. Цементации подвергают такие изделия, которые работают одновременно на
истирание и удар.
Существуют
два вида цементации: цементация твердым карбюризатором и газовая цементация.
При
цементации твердым карбюризатором применяют древесный уголь в смеси с
углекислыми солями — карбонатами (ВаСО3, Nа2СО3, К2СО3, СаСО3 и др.).
Цементации
подвергают заготовки из углеродистой или легированной стали с массовым
содержанием углерода до 0,08 %. Для деталей, подверженных большим напряжениям,
применяют стали, содержащие до 0,3 % С. Такое содержание углерода обеспечивает
высокую вязкость сердцевины после цементации.
Для
цементации заготовки помещают в стальные цементационные ящики, засыпают
карбюризатором, покрывают крышками, тщательно обмазывают щели глиной, помещают
ящики в печь и выдерживают там 5—10 ч при температуре 930—950 °С.
Технология
цементации деталей в твердом карбюризаторе заключается в следующем. Детали
очищают от грязи, масла, окалины и упаковывают в цементационный ящик. На дно
ящика насыпают карбюризатор слоем 25—30 мм,
на
него укладывают первый ряд деталей.
Расстояние
между деталями должно быть 15—20 мм, а
между деталями и стенкой ящика 15—25 мм.
На первый ряд деталей насыпают
карбюризатор и укладывают следующий ряд
деталей, снова засыпают карбюризатор, и
так до заполнения ящика до верха. Сверху
ящик закрывают крышкой и обмазывают
глиной (рис. 3).
Рис.
3. Упаковка деталей в цементационный ящик:
1
— ящик; 2 — карбюризатор; 8 — «свидетели»; 4 — детали.
При
нагревании в присутствии угля углекислый барий при температуре 900 °С распадается
по реакции
ВаСО3
+ С ®
ВаО + 2СО.
В
результате образуется оксид углерода, который на поверхности стальных заготовок
диссоциирует с выделением активного атомарного углерода; этот углерод
адсорбируется и диффундирует в поверхностный слой заготовки, в результате
повышается его массовое содержание в аустените, далее по достижении предела
растворимости образуется цементит
3Fe
+ С ®
Fe3С.
Поверхности,
не подлежащие цементации, изолируют от карбюризатора нанесением на них обмазок
или омедняют электролитическим способом. Глубина цементации обычно составляет
0,5—3 мм; цементированные заготовки содержат в поверхностном слое 0,95— 1,1 %
С.
При
газовой цементации в качестве карбюризатора применяют различные газы и газовые смеси
(природный, светильный, генераторный газы и др.). В их состав кроме оксида
углерода входят углеводороды, из которых особое значение имеет метан СН4.
Газовую цементацию выполняют в герметически закрытых безмуфельных или муфельных
печах непрерывного действия при температуре 900— 950 °С и непрерывном потоке
цементирующего газа или в шахтных печах периодического действия. В шахтных
печах для цементации используют жидкие углеводороды (керосин, синтин), которые
каплями подаются в печь и, испаряясь, образуют газы- карбюризаторы.
Преимуществом
газовой цементации перед цементацией твердым карбюризатором являются
двух-трехкратное ускорение процесса, чистота рабочего места, возможность
лучшего управления процессом. Газовая цементация применяется очень широко.
Цементированные
заготовки подвергают однократной или двойной закалке и низкому отпуску.
Однократную закалку с нагревом до 820—850 °С применяют в большинстве случаев,
особенно для наследственно-мелкозернистых сталей, когда продолжительная
вы-держка в горячей печи при цементации не сопровождается большим ростом зёрен
аустенита. Такая закалка обеспечивает частичную перекристаллизацию и
измельчение зерна сердцевины заготовки, а также измельчение зерна и полную
закалку цементированного слоя. Закалка после газовой цементации часто
производится из цементационной печи после подструживания заготовок до 840— 860
°С.
Двойную
закалку применяют, когда нужно получить высокую ударную вязкость и твёрдость
поверхностного слоя (например, для зубчатых колес). При этом производят;
I)
закалку пли нормализацию с нагревом до температуры 880- 9000 С для исправления
структуры сердцевины и ликвидации (растворения) цементитной сетки
поверхностного слоя; 2) закалку с нагревом до температуры 760— 780 °С для
измельчения структуры цементированного слоя и придания ему высокой твердости
(до 60—64 HRC для углеродистой стали). Закаленные заготовки подвергают низкому
отпуску (150— 170 °С).
Углеродистая
сталь имеет очень большую критическую скорость закалки, и сердцевина заготовок
из такой стали независимо от скорости охлаждения имеет структуру перлит +
феррит. Поэтому, чтобы получить детали с сердцевиной высокой прочности (сорбит
+ феррит), применяют легированную сталь, имеющую меньшую критическую скорость
закалки (например, сталь марок 20Х, 18ХГТ, 25ХГМ и др.).
Азотирование.
Цель азотирования — придание поверхностному слою деталей высокой твердости,
износостойкости и коррозионной стойкости. Азотирование осуществляется при
выделении активного азота из диссоциирующего аммиака
2NH3
®
2N + ЗН2.
Азотируют
легированную сталь, содержащую алюминий, титан, вольфрам, ванадий, молибден или
хром (например, сталь марок 35ХМЮА, 35ХЮА и др.).
Перед
азотированием заготовки подвергают закалке и высокому отпуску. Азотирование
производят в печах при температуре 500— 600 °С. Активный азот, выделяющийся при
диссоциации аммиака, диффундирует в поверхностный слой и вместе с
перечисленными легирующими элементами и железом образует очень твердые
химические соединения — нитриды (A1N, MoN, Fe3N и др.).
Азотирование
на глубину 0,2—0,5 мм продолжается 25—60 ч и в этом его основной недостаток.
Однако азотирование имеет ряд преимуществ перед цементацией: температура
нагрева сравнительно низкая, а твердость более высокая (1100—1200 по Виккерсу,
вместо 800—900 после цементации и закалки); у азотированных изделий большие
коррозионная стойкость, сопротивление усталости и меньшая хрупкость. Поэтому
азотирование широко применяют для деталей из стали и чугуна (шестерен,
коленчатых валов, цилиндров двигателей внутреннего сгорания и т. д.).
Азотирование
приводит к некоторому увеличению размеров заготовок, поэтому после азотирования
их подвергают шлифованию.
Цианирование.
Цианирование — насыщение поверхностного слоя одновременно углеродом и азотом;
оно бывает жидкостным и газовым.
Жидкостное
цианирование производится в ваннах с расплавами цианистых солей (NaCН, KCН,
Са(CN)2., и др.) при температуре, достаточной для разложения их с выделением
активных атомов Си N.
Низкотемпературное
(550—600 °С) цианирование применяют главным образом для инструментов из
быстрорежущей стали с целью повышения их стойкости и производится в расплавах
чистых цианистых солей. Высокотемпературное (800—850 °С) цианирование
осуществляется в ваннах, содержащих 20—40 %-ные расплавы цианистых солей с
нейтральными солями (NaCl, Na.2CO3 и др.) для повышения температуры плавления
ванны. Продолжительность жидкостного цианирования от 5 мин до 1 ч. Глубина
цианирования 0,2—0,5 мм.
После
цианирования заготовки подвергают закалке и низкому отпуску. Цианирование, как
и цементацию, применяют для различных изделий, при этом коробление заготовок
значительно меньше, чем при цементации, а износо- и коррозионная стойкость
более высокие. Недостатком жидкостного цианирования является ядовитость
цианистых солей, а также их высокая стоимость.
Газовое
цианирование отличается от газовой цементации тем, что к цементирующему газу
добавляют аммиак, дающий активизированные атомы азота. Газовое цианирование, так
же как и жидкостное, разделяется на низкотемпературное и высокотемпературное.
При
низкотемпературном (500—700 °С) газовом цианировании в сталь преимущественно
диффундирует азот (с образованием нитридов), а углерод диффундирует в малых
количествах. Это цианирование так же как и жидкостное низкотемпературное,
применяют для обработки инструментов из быстрорежущей стали.
При
высокотемпературном газовом цианировании (800—850 °С) в сталь диффундирует
значительное количество углерода с образованием аустенита. После
высокотемпературного цианирования заготовки закаливают.
При
газовом цианировании, называемом также нитроцементацией, отпадает необходимость
в применении ядовитых солей и, кроме того, имеется возможность обработки более
крупных деталей.
Диффузионная
металлизация. Наиболее распространенными видами диффузионной металлизации
являются алитирование, хромирование, силицирование.
Алитирование
представляет собой поверхностное насыщение стальных и чугунных заготовок
алюминием с образованием твердого раствора алюминия в железе. Его применяют
преимущественно для деталей, работающих при высоких температурах (колосников,
дымогарных труб и др.), так как при этом значительно (до 10000С) повышается
жаростойкость стали.
Для
алитирования алюминий сначала наносят на заготовку распылением жидкой струи
сжатым воздухом, затем нанесенный слой алюминия защищают жаростойкой обмазкой и
производят диффузионный отжиг заготовок при температуре 920 °С в течение 3 ч. В
процессе отжига поверхностный слой заготовки насыщается алюминием на глубину в
среднем 0,5 мм.
Диффузионное
хромирование производится в порошковых смесях, составленных из феррохрома и
шамота, смоченных соляной кислотой или в газовой среде при разложении паров
хлорида хрома СrCl2. Хромированию подвергаются в основном стали с массовым
содержанием углерода не более 0,2 %. Хромированный слой низкоуглеродистой стали
незначительно повышает твердость, но обладает большой вязкостью, что позволяет
подвергать хромированные детали сплющиванию, прокатке и т. п. Хромированные
детали имеют высокую коррозионную стойкость в некоторых агрессивных средах
(азотной кислоте, морской воде). Это позволяет заменять ими детали из
дефицитной высокохромовой стали.
Силицирование
— насыщение поверхностного слоя стальных заготовок кремнием, обеспечивающее
повышение стойкости против коррозии и эрозии в морской воде, азотной, серной и
соляной кислотах, применяется для деталей, используемых в химической
промышленности.
Силицированный
слой представляет собой твердый раствор кремния в a-железе. Существует
силицирование в порошкообразных смесях ферросилиция, а также газовое
силицирование в среде хлорида кремния SiCl4.
3. Композиционные материалы.
Композиционные
материалы (композиты) состоят из химически разнородных компонентов,
нерастворимых друг в друге и связанных между собой в результате адгезии.
Основой композитов является пластическая матрица, которая связывает
наполнители, определяет форму изделия, его монолитность, теплофизические,
электро- и радиотехнические свойства, герметичность, химическую стойкость, а
также распределение напряжений между наполнителями.
В
качестве матрицы применяют металлы (алюминий, магний, их сплавы), полимеры
(эпоксидные, фенолформальдегидные смолы, полиамиды), керамические, углеродные
материалы.
Наполнители
чаще всего играют роль упрочнителей, воспринимают основную долю нагрузки и
определяют модуль упругости и твердость композита, а иногда также фрикционные,
магнитные, теплофизические и электрические свойства. Наполнителями служат
тонкая (диаметром несколько микрометров) проволока из высокопрочной стали,
вольфрама, титана, а также стеклянные, полиамидные, углеродные, боридные
волокна и волокна на основе нитевидных кристаллов (оксидов, карбидов, боридов,
нитридов) и др.
Композиты
получают пропиткой наполнителей матричным раствором, нанесением материала
матрицы на волокна плазменным напылением, электрохимическим способом, введением
тугоплавких наполнителей в расплавленный материал матрицы, прессованием,
спеканием.
Композиционные
материалы с металлической матрицей
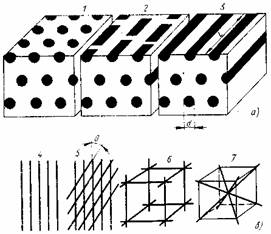
Рис.4.
Схема структуры (а) и армирования непрерывными волокнами (б) композиционных
материалов
Композиционные
материалы состоят из металлической матрицы (чаще Al, Mg, Ni и их сплавы),
упрочненной высокопрочным волокнами (волокнистые материалы) или
тонкодисперсными тугоплавкими частицами, не растворяющимися в основном металле
(дисперсно-упрочненные материалы). Металлическая матрица связывает волокна
(дисперсные частицы) в единое целое. Волокно (дисперсные частицы) плюс связка
(матрица), составляющие или иную композицию, получили название композиционные
материалы (рис.4).
3.1. Волокнистые композиционные материалы.
На
рис.4 приведены схемы армирования волокнистых композиционных материалов. Композиционные
материалы с волокнистым наполнителем (упрочнителем) по механизму армирующего действия
делят на дискретные, в которых отношение длины волокна к диаметру l/d ≈
10÷103, и с непрерывным волокном, в которых l/d = ∞. Дискретные
волокна располагаются в матрице хаотично. Диаметр волокон от долей до сотен
микрометров. Чем больше отношение длины к диаметру волокна, тем выше степень
упрочнения.
Часто
композиционный материал представляет собой слоистую структуру, в которой каждый
слой армирован большим числом параллельных непрерывных волокон. Каждый слой
можно армировать также непрерывными волокнами, сотканными в ткань, которая
представляет собой исходную форму, по ширине и длине соответствующую конечному
материалу. Нередко волокна сплетают в трехмерные структуры.
Композиционные
материалы отличаются от обычных сплавов более высокими значениями временного
сопротивления и предела выносливости (на 50–100 %), модуля упругости,
коэффициента жесткости (Е/γ) и пониженной склонностью к
трещинообразованию. Применение композиционных материалов повышает жесткость
конструкции при одновременном снижении ее металлоемкости.
Таблица1.
Механические свойства композиционных материалов на металлической основе
Материал
|
σВ
|
σ-1
|
Е, ГПа
|
σВ/γ
|
Е/γ
|
МПа
|
Бор–алюминий (ВКА–1А)
|
1300
|
600
|
220
|
500
|
84,6
|
Бор–магний (ВКМ–1)
|
1300
|
500
|
220
|
590
|
100
|
Алюминий–углерод (ВКУ–1)
|
900
|
300
|
220
|
450
|
100
|
Алюминий–сталь (КАС–1А)
|
1700
|
350
|
110
|
370
|
24,40
|
Никель–вольфрам (ВКН–1)
|
700
|
150
|
–
|
–
|
–
|
Прочность
композиционных (волокнистых) материалов определяется свойствами волокон;
матрица в основном должна перераспределять напряжения между армирующими элементами.
Поэтому прочность и модуль упругости волокон должны быть значительно больше,
чем прочность и модуль упругости матрицы. Жесткие армирующие волокна
воспринимают напряжения, возникающие в композиции при нагружении, придают ей
прочность и жесткость в направлении ориентации волокон.
Для
упрочнения алюминия, магния и их сплавов применяют борные (σВ =
2500÷3500 МПа, Е = 38÷420 ГПа) и углеродные (σВ =
1400÷3500 МПа, Е = 160÷450 ГПа) волокна, а также волокна из
тугоплавких соединений (карбидов, нитридов, боридов и оксидов), имеющих высокие
прочность и модуль упругости. Так, волокна карбида кремния диаметром 100 мкм
имеют σВ = 2500÷3500 МПа, Е = 450 ГПа. Нередко используют в
качестве волокон проволоку из высокопрочных сталей.
Для
армирования титана и его сплавов применяют молибденовую проволоку, волокна
сапфира, карбида кремния и борида титана.
Повышение
жаропрочности никелевых сплавов достигается армированием их вольфрамовой или
молибденовой проволокой. Металлические волокна используют и в тех случаях, когда
требуются высокие теплопроводность и электропроводимость. Перспективными
упрочнителями для высокопрочных и высокомодульных волокнистых композиционных
материалов являются нитевидные кристаллы из оксида и нитрида алюминия, карбида
и нитрида кремния, карбида бора и др., имеющие σВ = 15000÷28000 МПа
и Е = 400÷600 ГПа.
В
табл.1 приведены свойства некоторых волокнистых композиционных материалов.
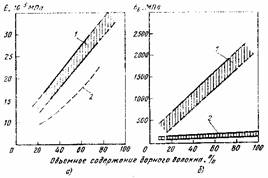
Рис.5.
Зависимость модуля упругости Е (а) и временного сопротивления σВ (б)
бороалюминиевого композиционного материала вдоль (1) и поперек (2) оси
армирования от объемного содержания борного волокна
Композиционные
материалы на металлической основе обладают высокой прочностью (σВ,
σ-1) и жаропрочностью, в то же время они малопластичны. Однако волокна в
композиционных материалах уменьшают скорость распространения трещин,
зарождающихся в матрице, и практически полностью исключают внезапное хрупкое
разрушение. Отличительной особенностью одноосных волокнистых композиционных
материалов являются анизотропия механических свойств вдоль к поперек волокон и
малая чувствительность к концентраторам напряжения,
На
рис.5 приведена зависимость σВ и Е бороалюминиевого композиционного
материала от содержания борного волокна вдоль (1) и поперек (2) оси армирования.
Чем больше объемное содержание волокон, тем выше σВ, σ-1 и Е вдоль
оси армирования. Однако необходимо учитывать, что матрица может передавать
напряжения волокнам только в том случае, когда существует прочная связь на
поверхности раздела армирующее волокно — матрица. Для предотвращения контакта
между волокнами матрица должна полностью окружать все волокна, что достигается
при содержании ее не менее 15–20 %.

Рис.6.
Длительная прочность бороалюминиевого композиционного материала, содержащего
50% борного волокна, в сравнении с прочностью титановых сплавов (а) и
длительная прочность никелевого композиционного материала в сравнении с
прочностью дисперсионно-твердеющих сплавов (б)
Матрица
и волокно не должны между собой взаимодействовать (должна отсутствовать
взаимная диффузия) при изготовлении или эксплуатации, так как это может
привести к понижению прочности композиционного материала.
Анизотропия
свойств волокнистых композиционных материалов учитывается при конструировании деталей
для оптимизации свойств путем согласования поля сопротивления с полями
напряжения.
Армирование
алюминиевых, магниевых и титановых сплавов непрерывными тугоплавкими волокнами
бора, карбида кремния, диборида титана и оксида алюминия значительно повышает
жаропрочность. Особенностью композиционных материалов является малая скорость
разупрочнения во времени (рис.6, а) с повышением температуры.
Основным
недостатком композиционных материалов с одно- и двумерным армированием является
низкое сопротивление межслойному сдвигу и поперечному обрыву. Этого недостатка
лишены материалы с объемным армированием.
3.2. Дисперсно-упрочненные композиционные материалы.
В
отличие от волокнистых композиционных материалов в дисперсно-упрочненных
композиционных материалах матрица является основным элементом, несущим
нагрузку, а дисперсные частицы тормозят движение в ней дислокаций. Высокая
прочность достигается при размере частиц 10–500 нм при среднем расстоянии между
ними 100–500 нм и равномерном распределении их в матрице. Прочность и
жаропрочность в зависимости от объемного содержания упрочняющих фаз не
подчиняются закону аддитивности. Оптимальное содержание второй фазы для
различных металлов неодинаково, но обычно не превышает 5–10об.%.
Использование
в качестве упрочняющих фаз стабильных тугоплавких соединений (оксиды тория,
гафния, иттрия, сложные соединения оксидов и редкоземельных металлов),
нерастворяющихся в матричном металле, позволяет сохранить высокую прочность
материала до 0,9–0,95Тпл. В связи с этим такие материалы чаще применяют как
жаропрочные. Дисперсноупрочненные композиционные материалы могут быть получены
на основе большинства применяемых в технике металлов и сплавов.
Наиболее
широко используют сплавы на основе алюминия – САП (спеченный алюминиевый
порошок). САП состоит из алюминия и дисперсных чешуек А12О3. Частицы А12О3
эффективно тормозят движение дислокаций и тем самым повышают прочность сплава.
Содержание А12О3 в САП колеблется от 6–9 % (САП-1) и до 13–18 % (САП-3). С
увеличением содержания А12О3 σB повышается от 300 для САП-1 до 400 МПа для
САП-3, а относительное удлинение соответственно снижается с 8 до 3%. Плотность
этих материалов равна плотности алюминия, они не уступают ему по коррозионной
стойкости и даже могут заменять титан и коррозионно-стойкие стали при работе в
интервале температур 250–500°С. По длительной прочности они превосходят
деформируемые алюминиевые сплавы. Длительная прочность σ100 для сплавов
САП-1 и САП-2 при 500°С составляет 45–55 МПа.
Большие
перспективы у никелевых дисперсно-упрочненных материалов. Наиболее высокую
жаропрочность имеют сплавы на основе никеля с 2–З об.% двуоксида тория или
двуоксида гафния. Матрица этих сплавов обычно γ-твердый раствор Ni+20% Cr,
Ni+15% Mo, Ni+20% Cr и Мо. Широкое применение получили сплавы ВДУ-1 (никель,
упрочненный двуокисью тория), ВДУ-2 (никель, упрочненный двуокисью гафния) и
ВД-3 (матрица Ni+20% Сг, упрочненная окисью тория). Эти сплавы обладают высокой
жаропрочностью. При температуре 1200°С сплав ВДУ-1 имеет σ100≈75 МПа
и σ1000≈65 МПа, сплав ВД-3 – 65 МПа. Дисперсно-упрочненные
композиционные материалы, так же как волокнистые, стойки к разупрочнению с
повышением температуры и длительности выдержки при данной температуре (см.
рис.6).
Области
применения композиционных материалов не ограничены. Они применяются в авиации
для высоконагруженных деталей самолетов (обшивки, лонжеронов, нервюр, панелей и
т.д.) и двигателей (лопаток компрессора и турбины и т.д.), в космической
технике для узлов силовых конструкций аппаратов, подвергающихся нагреву, для
элементов жидкости, для элементов жесткости, панелей, в автомобилестроении для
облегчения кузовов, рессор, рам, панелей кузовов, бамперов и т.д., в горной
промышленности (буровой инструмент, детали комбайнов и т.д.), в гражданском
строительстве (пролеты мостов, элементы сборных конструкций высотных сооружений
и т.д.) и в других областях народного хозяйства.
Применение
композиционных материалов обеспечивает новый качественный скачок в увеличении
мощности двигателей, энергетических и транспортных установок, уменьшении массы
машин и приборов.
Технология
получения полуфабрикатов и изделий из композиционных материалов достаточно
хорошо отработана.
Композиционные материалы с неметалической матрицей
3.3. Общие сведения, состав и классификация
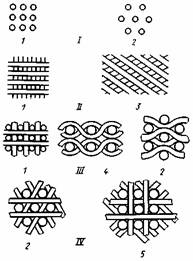
Рис.8.
Схемы армирования композиционных материалов
Композиционные
материалы с неметаллической матрицей нашли широкое применение. В качестве
неметаллических матриц используют полимерные, углеродные и керамические
материалы. Из полимерных матриц наибольшее распространение получили эпоксидная,
фенолоформальдегидная и полиимидная. Угольные матрицы коксованные или
пироуглеродные получают из синтетических полимеров, подвергнутых пиролизу.
Матрица связывает композицию, придавая ей форму. Упрочнителями служат волокна:
стеклянные, углеродные, борные, органические, на основе нитевидных кристаллов
(оксидов, карбидов, боридов, нитридов и др.), а также металлические
(проволоки), обладающие высокой прочностью и жесткостью.
Свойства
композиционных материалов зависят от состава компонентов, их сочетания,
количественного соотношения и прочности связи между ними. Армирующие материалы
могут быть в виде волокон, жгутов, нитей, лент, многослойных тканей.
Содержание
упрочнителя в ориентированных материалах составляет 60–80 об.%, в
неориентированных (с дискретными волокнами и нитевидными кристаллами) – 20–30
об.%. Чем выше прочность и модуль упругости волокон, тем выше прочность и
жесткость композиционного материала. Свойства матрицы определяют прочность
композиции при сдвиге и сжатии и сопротивление усталостному разрушению.
По
виду упрочнителя композиционные материалы классифицируют на стекловолокниты,
карбоволокниты с углеродными волокнами, бороволокниты и органоволокниты.
В
слоистых материалах волокна, нити, ленты, пропитанные связующим, укладываются
параллельно друг другу в плоскости укладки. Плоскостные слои собираются в
пластины. Свойства получаются анизотропными. Для работы материала в изделии
важно учитывать направление действующих нагрузок. Можно создавать материалы как
с изотропными, так и с анизотропными свойствами. Можно укладывать волокна под
разными углами, варьируя свойства композиционных материалов. От порядка укладки
слоев по толщине пакета зависят изгибные и крутильные жесткости материала.
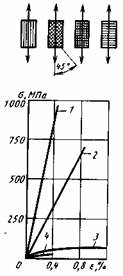
Рис.7.
Зависимость между напряжением и деформацией при растяжении эпоксидного
углепластика с различной схемой укладки упрочнителя: 1 – продольная; 2 – под
углом 45º; 3 – взаимно перпендикулярная; 4 – поперечная
Применяется
укладка упрочнителей из трех, четырех и более нитей (рис.7). Наибольшее
применение имеет структура из трех взаимно перпендикулярных нитей. Упрочнители
могут располагаться в осевом, радиальном и окружном направлениях.
Трехмерные
материалы могут быть любой толщины в виде блоков, цилиндров. Объемные ткани
увеличивают прочность на отр ыв и сопротивление сдвигу по сравнению со
слоистыми. Система из четырех нитей строится путем расположения упрочнителя по
диагоналям куба. Структура из четырех нитей равновесна, имеет повышенную жесткость
при сдвиге в главных плоскостях. Однако создание четырехнаправленных материалов
сложнее, чем трех-направленных. Зависимость механических свойств композиционных
материалов от схемы армирования приведена на рис.8.
3.4. Карбоволокниты
Карбоволокниты
(углепласты) представляют собой композиции, состоящие из полимерного связующего
(матрицы) и упрочнителей в виде углеродных волокон (карбоволокон).
Высокая
энергия связи С–С углеродных волокон позволяет им сохранять прочность при очень
высоких температурах (в нейтральной и восстановительной средах до 2200°С), а
также при низких температурах. От окисления поверхности волокна предохраняют
защитными покрытиями (пиролитическими). В отличие от стеклянных волокон
карбоволокна плохо смачиваются связующим (низкая поверхностная энергия),
поэтому их подвергают травлению. При этом увеличивается степень активирования
углеродных волокон по содержанию карбоксильной группы на их поверхности.
Межслойная прочность при сдвиге углепластиков увеличивается в 1,6–2,5 раза.
Применяется вискеризация нитевидных кристаллов TiO2, AlN и Si3N4, что дает
увеличение межслойной жесткости в 2 раза и прочности в 2,8 раза. Применяются
пространственно армированные структуры.
Связующими
служат синтетические полимеры (полимерные карбоволокниты); синтетические
полимеры, подвергнутые пиролизу (коксованные карбоволокниты); пиролитический
углерод (пироуглеродные карбоволокниты).
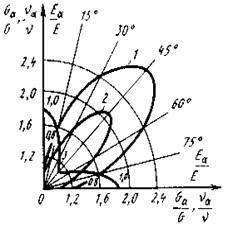
Рис.9.
Значения модулей упругости (1), сдвига (2) и коэффициентов Пуассона (3) под
углом к главному направлению композиционного материала, образованного системой
трех нитей
Эпоксифенольные
карбоволокниты КМУ-1л, упрочненный углеродной лентой, и КМУ-ly на жгуте,
вискеризованном нитевидными кристаллами, могут длительно работать при
температуре до 200°С.
Карбоволокниты
КМУ-3 и КМУ-Зл получают на эпоксиани-линоформальдегидном связующем, их можно
эксплуатировать при температуре до 100°С, они наиболее технологичны.
Карбоволокниты КМУ-2 и КМУ-2л на основе полиимидного связующего можно применять
при температуре до 300°С.
Карбоволокниты
отличаются высоким статическим и динамическим сопротивлением усталости (рис.9),
сохраняют это свойство при нормальной и очень низкой температуре (высокая
теплопроводность волокна предотвращает саморазогрев материала за счет внутреннего
трения). Они водо- и химически стойкие. После воздействия на воздухе
рентгеновского излучения σИЗГ и Е почти не изменяются.
Теплопроводность
углепластиков в 1,5–2 раза выше, чем теплопроводность стеклопластиков. Они
имеют следующие электрические свойства: ρV=0,0024÷0,0034 Ом∙см
(вдоль волокон); е=10 и tgδ=0,01 (при частоте тока 1010 Гц).
Карбостекловолокниты
содержат наряду с угольными стеклянные волокна, что удешевляет материал.
Зависимость механических свойств модифицированного карбоволокнита от содержания
углеродных волокон показана на рис.10.
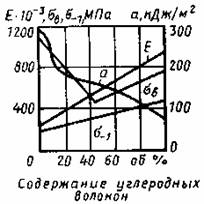
Рис.10.
Зависимость модуля упругости Е, предела прочности σВ, ударной вязкости а и
сопротивления усталости σ-1 карбостекловолокнита от содержания углеродных
волокон (общее содержание наполнителя в композиции 62 об.%)
3.5. Карбоволокниты с углеродной матрицей.
Коксованные
материалы получают из обычных полимерных карбоволокнитов, подвергнутых пиролизу
в инертной или восстановительной атмосфере. При температуре 800–1500°С образуются
карбонизированные, при 2500–3000°С графитированные карбоволокниты. Для
получения пироуглеродных материалов упрочнитель выкладывается по форме изделия
и помещается в печь, в которую пропускается газообразный углеводород (метан).
При определенном режиме (температуре 1100°С и остаточном давлении 2660 Па)
метан разлагается и образующийся пиролитический углерод осаждается на волокнах
упрочнителя, связывая их.
Образующийся
при пиролизе связующего кокс имеет высокую прочность сцепления с углеродным
волокном. В связи с этим композиционный материал обладает высокими
механическими и абляционными свойствами, стойкостью к термическому удару.
Карбоволокнит
с углеродной матрицей типа КУП-ВМ по значениям прочности и ударной вязкости в
5–10 раз превосходит специальные графиты; при нагреве в инертной атмосфере и
вакууме он сохраняет прочность до 2200°С, на воздухе окисляется при 450°С и
требует защитного покрытия. Коэффициент трения одного карбоволокнита с
углеродной матрицей по другому высок (0,35–0,45), а износ мал (0,7–1 мкм на
торможение).
Полимерные
карбоволокниты используют в судо- и автомобилестроении (кузова гоночных машин,
шасси, гребные винты); из них изготовляют подшипники, панели отопления,
спортивный инвентарь, части ЭВМ. Высокомодульные карбоволокниты применяют для
изготовления деталей авиационной техники, аппаратуры для химической
промышленности, в рентгеновском оборудовании и др.
Карбоволокниты
с углеродной матрицей заменяют различные типы графитов. Они применяются для
тепловой защиты, дисков авиационных тормозов, химически стойкой аппаратуры.
3.6.
Бороволокниты
Бороволокниты
представляют собой композиции из полимерного связующего и упрочнителя — борных
волокон.
Бороволокниты
отличаются высокой прочностью при сжатии, сдвиге и срезе, низкой ползучестью,
высокими твердостью и модулем упругости, теплопроводностью и
электропроводимостью. Ячеистая микроструктура борных волокон обеспечивает
высокую прочность при сдвиге на границе раздела с матрицей.
Помимо
непрерывного борного волокна применяют комплексные боростеклониты, в которых
несколько параллельных борных волокон оплетаются стеклонитью, придающей
формоустойчивость. Применение боростеклонитей облегчает технологический процесс
изготовления материала.
В
качестве матриц для получения бороволокнитов используют модифицированные
эпоксидные и полиимидные связующие. Бороволокниты КМБ-1 и КМБ-1к предназначены
для длительной работы при температуре 200°С; КМБ-3 и КМБ-Зк не требуют высокого
давления при переработке и могут работать при температуре не свыше 100°С;
КМБ-2к работоспособен при 300°С.
Влияние
на механические свойства бороволокнита содержания волокна приведено на рис.11,
а влияние различных матриц – на рис.12.
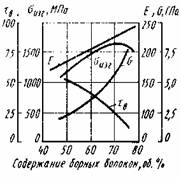
Рис.11.
Зависимость механических свойств бороволокнита КМБ-1 от содержания борного
волокна:
Е
– модуль упругости;
σИЗГ
– предел прочности при изгибе;
G
– модуль сдвига;
τВ
– предел прочности при сдвиге
Бороволокниты
обладают высокими сопротивлениями усталости, они стойки к воздействию радиации,
воды, органических растворителей и горючесмазочных материалов.
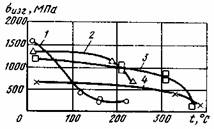
Рис.12.
Зависимость разрушающего напряжения при изгибе бороволокнитов на различных
связующих от температуры: 1, 2 – эпоксидное; 3 – полиимидное; 4 –
кремнийорганическое связующее
Поскольку
борные волокна являются полупроводниками, то бороволокниты обладают повышенной
теплопроводностью и электропроводимостью: λ=43 кДж/(м∙К); α=4∙10-6
С-1 (вдоль волокон); ρV=1,94∙107 Ом∙см; е=12,6÷20,5
(при частоте тока 107 Гц); tgδ=0,02÷0,051 (при частоте тока 107
Гц). Для бороволокнитов прочность при сжатии в 2–2,5 раза больше, чем для
карбоволокнитов.
Изделия
из бороволокнитов применяют в авиационной и космической технике (профили,
панели, роторы и лопатки компрессоров, лопасти винтов и трансмиссионные валы
вертолетов и т.д.).
3.7. Органоволокниты
Органоволокниты
представляют собой композиционные материалы, состоящие из полимерного
связующего и упрочнителей (наполнителей) в виде синтетических волокон. Такие
материалы обладают малой массой, сравнительно высокими удельной прочностью и
жесткостью, стабильны при действии знакопеременных нагрузок и резкой смене
температуры. Для синтетических волокон потери прочности при текстильной
переработке небольшие; они малочувствительны к повреждениям.
В
органоволокнитах значения модуля упругости и температурных коэффициентов
линейного расширения упрочнителя и связующего близки. Происходит диффузия
компонентов связующего в волокно и химическое взаимодействие между ними.
Структура материала бездефектна. Пористость не превышает 1–3% (в других
материалах 10–20%). Отсюда стабильность механических свойств органоволокнитов
при резком перепаде температур, действии ударных и циклических нагрузок.
Ударная вязкость высокая (400–700 кДж/м2). Недостатком этих материалов является
сравнительно низкая прочность при сжатии и высокая ползучесть (особенно для
эластичных волокон).
Органоволокниты
устойчивы в агрессивных средах и во влажном тропическом климате;
диэлектрические свойства высокие, а теплопроводность низкая. Большинство
органоволокнитов может длительно работать при температуре 100–150°С, а на
основе полиимидного связующего и полиоксадиазольных волокон – при 200–300°С.
В
комбинированных материалах наряду с синтетическими волокнами применяют
минеральные (стеклянные, карбоволокна и бороволокна). Такие материалы обладают
большей прочностью и жесткостью.
Органоволокниты
применяют в качестве изоляционного и конструкционного материала в
электрорадиоиромышленности, авиационной технике, автостроении; из них
изготовляют трубы, емкости для реактивов, покрытия корпусов судов и др.
Список литературы
Гуляев
А.П. «Металловедение», М.: 1968.
Дальский
А.М. «Технология конструкционных материалов», М.: 1985.
Куманин
И.Б. «Литейное производство», М.: 1971.
Лахтин
Ю.М. «Материаловедение», М.: 1990.
Семенов
«Ковка и объемная штамповка», М.: 1972.
Никифоров
В.М. «Технология металлов и конструкционные материалы», Ленинград.: 1986.
|